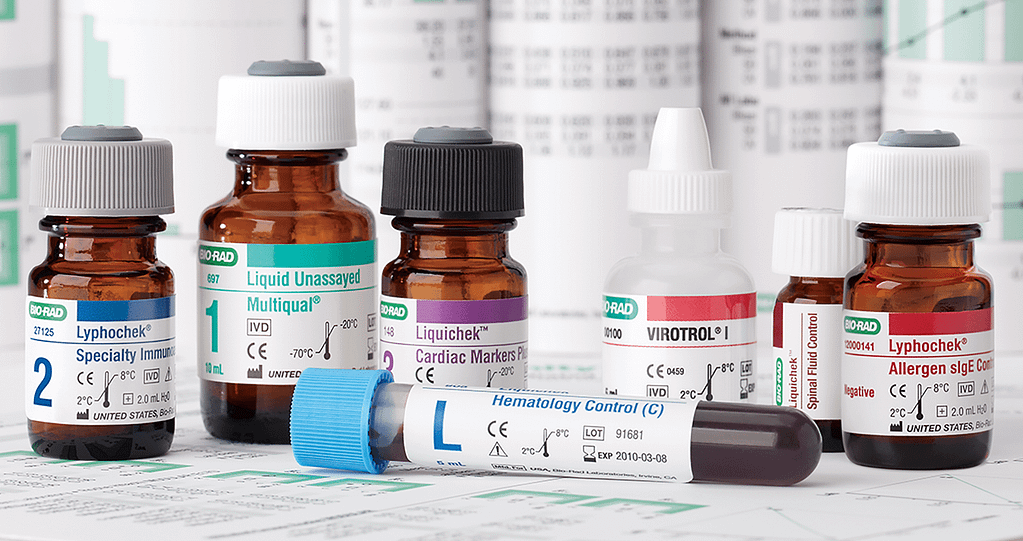
Controls have to be reconstituted as per instructions, given in the pack insert.
Step 1 : Ensure that The first time when you run a control, it is at Room Temperature.
Step 2 : If control is beyond one 2 SD , then rerun the same control after making sure it’s at room temperature.
Step 3 : If still out, then take a freshly reconstituted Control at room temperature and run that.
Step 4 : If Still Out, then Do a Delta Check by running previous day’s sample and compare the Bias ( has to be less than 10 % )
Bias is ( Run 2 – Run 1 ) ÷ ( Run 1 ) and multiplied by 100.
Step 5 : If still out, then Calibrate and rerun the control
Step 6 : If Still out, then Call the Application specialist.
Check Expiry of Reagents on board and instrument factors where necessary. Directly Going for Calibration when controls are out, is an incorrect process.
Make sure Lab mean is set, on 30, 60 & 90 points.
STEPS FOR ROOT CAUSE ANALYSIS
1) Check control material
Change in manufacturer Lot
Improper reconstitution of control
Expired control used
Inadequate storage
2) Check last calibration
Calibration as per frequency
Calibration signals & Variation
3) Check calibration material
Change in manufacturer Lot
Improper reconstitution
Expired calibrator used
Inadequate storage
4) Check Reagents
Change in manufacturer Lot
Improper reconstitution
Expired Reagent
Inadequate storage
Bubbles in reagent
5) Check Instruments
Untrained operator
Inadequate Daily Maintenance
Instrument Preventive maintenance
Instrument calibration
6) Check Trends
Compare data with peer group
Bottle mean/SD & Lab mean/SD Variation